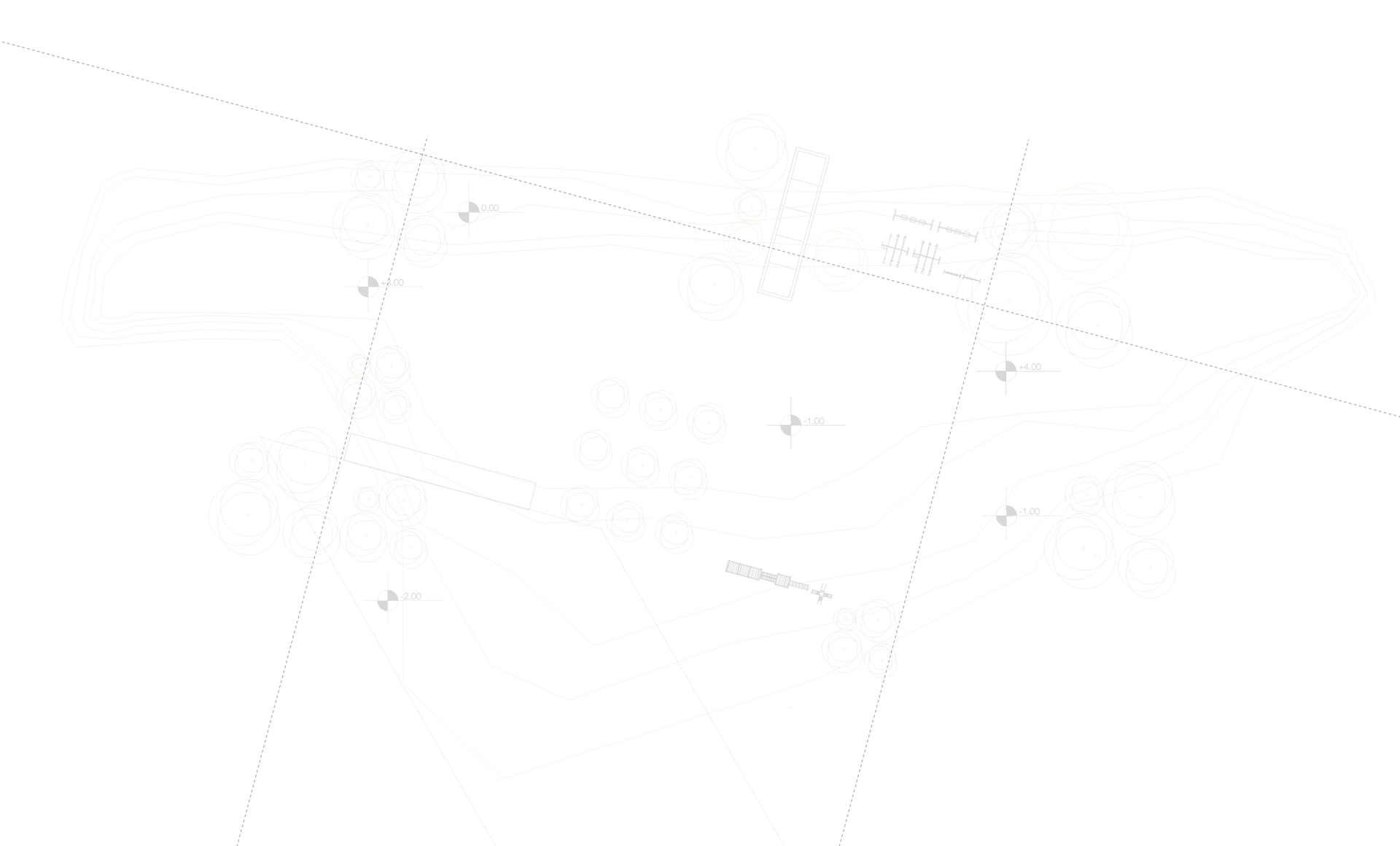





“ A maior habilidade de um líder é desenvolver habilidades extraordinárias em pessoas comuns.. ”
– Abraham Lincoln
O que é Pultrusão ?
Pultrusão é um processo contínuo para fabricação de materiais compósitos com seção transversal constante. O termo é uma palavra de junção, combinando "puxar" e "extrusão". Ao contrário da extrusão, que empurra o material, a pultrusão funciona puxando o material.
História
Uma patente de tipo pultrus muito inicial foi apresentada por J.H. Watson em 1944. Isto foi seguido pelo arquivamento de M. J. Meek em 1950. As primeiras pultrusões comerciais foram fornecidas pela Glastic Company de Cleveland, Ohio sob a patente depositada em 1952 por Rodger B. White. A patente concedida a W. B. Goldsworthy em 1959 ajudou a iniciar a promoção e disseminação de conhecimento dentro da indústria. W. Brandt Goldsworthy é amplamente considerado o inventor da pultrusão. [1]
Paralelamente ao trabalho de Goldsworthy, que concentrou seu trabalho em resinas de poliéster insaturado, a Ernst Kühne na Alemanha desenvolveu um processo bastante similar em 1954 com base em resina epóxi.
A invenção, o desenvolvimento e a emissão de patentes continuam no campo da pultrusão até hoje. Uma inovação posterior neste campo foi desenvolvida e patenteada pela Thomas GmbH + Co. Technik + Innovation KG na Alemanha em 2008 e é descrita abaixo.
Processo
1 - rolo contínuo de fibras reforçadas / tapete de fibra tecida
2 - Rolo de tensão
3 - Impregnadora de Resina
4 - Fibra embebida em resina
5 - Morrer e fonte de calor
6 - mecanismo de tração
7 - Polímero reforçado com fibra endurecida
No processo de pultrusão padrão, os materiais de reforço, como fibras ou fios trançados ou trançados, são impregnados com resina, possivelmente seguidos por um sistema pré-formado separado, e puxados através de uma matriz estacionária aquecida onde a resina sofre polimerização. A impregnação é feita puxando o reforço através de um banho ou injectando a resina numa câmara de injecção que está tipicamente ligada à matriz. Muitos tipos de resina podem ser usados em pultrusão, incluindo poliéster, poliuretano, viniléster e epóxi. A resina fornece a resistência ao meio ambiente (isto é, a resistência à corrosão, a resistência aos raios UV, a resistência ao impacto, etc.) e o vidro proporciona resistência, além da segurança contra incêndios. Um véu de superfície também pode ser adicionado para proteger contra a erosão ou “floração de fibra” e fornecer resistência à corrosão e resistência ultravioleta. A tecnologia não se limita a polímeros termoendurecíveis. Mais recentemente, a pultrusão tem sido usada com sucesso com matrizes termoplásticas, como o tereftalato de polibutileno (PBT), o tereftalato de polietileno (PET) por impregnação de pó da fibra de vidro ou envolvendo-a com material de folha da matriz termoplástica, que é então aquecida. A limpeza ecológica dos produtos manufaturados, em contraste com os compósitos na base de resinas termofixas, bem como as possibilidades praticamente ilimitadas de reciclagem (processamento) após o esgotamento dos recursos, parecem ser argumentos forçados em favor de termoplásticos reforçados. Por estas razões, a produção industrial e o uso dos materiais fornecidos em países altamente industrializados aumentaram de 8 a 10% ao ano nas últimas décadas. Novos desenvolvimentos (ver modificações no processo) que permitem que a fabricação não apenas de perfis retos, mas também curvos, estejam realmente pressionando a demanda por essa tecnologia, especialmente no setor automotivo. A tecnologia de pultrusão de fabricação de compósitos de fibra com matriz de polímero parece ser eficiente em termos de energia e economia de recursos. Fatores econômicos e ambientais favorecem o uso de uma matriz termoplástica, mas, devido à alta viscosidade das fusões, é difícil obter alta produtividade e alta qualidade de impregnação de fibras com esse tipo de matriz. Os produtos fabricados sob esta tecnologia são amplamente utilizados nas seguintes indústrias: - Nas indústrias agropecuárias e químicas, na fabricação de pisos resistentes quimicamente a meios agressivos, com características de resistência reforçada, utilizados na construção de instalações pecuárias, plantas químicas, etc .; - na indústria da construção, para a produção de armaduras de fibra de vidro, perfis, carcaças, barras de reforço para janelas de PVC, etc .; - na indústria aeroespacial para fabricação de componentes estruturais de aeronaves; - nas indústrias do desporto e do turismo, no fabrico de equipamento que apresente propriedades reforçadas de resistência: esquis, bastões de esqui, bandeiras de campos de golfe, construções de tendas e casebres, etc .; - na engenharia de energia elétrica para fabricação de estruturas dielétricas, hastes de fibra de vidro utilizadas em isoladores compostos e como estruturas de suporte para elementos de blocos de sinalização, e perfis de fibra de vidro utilizados na fabricação de transformadores e motores elétricos; - na produção comercial, utilizando grãos de material de moldagem de fibra longa (LLM) como matéria-prima para posterior fabricação de estruturas e produtos com maior resistência e propriedades químicas; - na indústria automotiva, para a produção de peças estruturais e complexas dos veículos com maior rigidez, rigidez e leveza; - e em muitas outras indústrias e fábricas, utilizando mecanismos, estruturas e materiais, que atendem a altos padrões de estabilidade química, dielétrica e de resistência.
Modificações no processo
Como os materiais são puxados através de uma matriz no processo de pultrusão padrão, o processo é adequado apenas para a fabricação de perfis retos.
Em uma modificação recentemente desenvolvida do processo, desenvolvida e patenteada pela Thomas GmbH + Co. Technik + Innovation KG, a matriz não é mais estacionária, mas se move para frente e para trás ao longo do perfil a ser fabricado. Este processo modificado, conhecido como "Radius-Pultrusion" permite também fabricar perfis curvos bi e tridimensionais. Ele também é beneficiado por várias tarefas no processo linear, especialmente se forem necessários reforços têxteis bastante complexos com baixa taxa de distorção
Equipamento
O design das máquinas de pultrusão varia. Dois tipos frequentemente usados são alternativos (mão-sobre-mão) e contínuos (cat-track).
Para o processo de pultrusão de raio, o layout das máquinas tem dois estágios móveis semelhantes à unidade de puxar mão sobre mão, mas como o processo é intermitente com apenas um extrator e o molde montado no palco de outro. Se as etapas estão se movendo linear ou circular depende do tipo de perfis a serem fabricados. O raio mínimo para uma máquina linear com estágios rotativos é de aprox. 2 m. Para raios menores, é necessário um movimento circular do molde e do estágio da pinça.
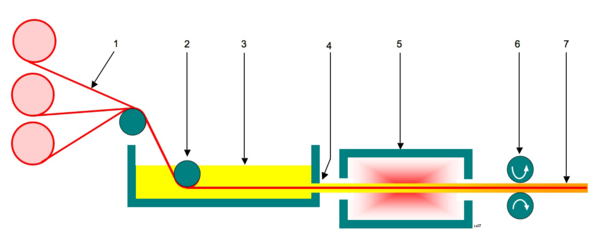